HS742 3D Cross-Hatch Sensor
PRODUCTS: HS742
The HS742 with Blue Laser Technology is a 3D Cross-Hatch sensor and is specifically used for measuring countersink alignment, fastener depth and dielectric fill height in the aerospace industry.
The HS742 DSP sensor with Blue Laser Technology is a 3D laser profiler housed in a totally self-contained, portable, handheld package. Expanding on the unique capabilities of the LaserGauge® line of DSP sensors, the HS742 utilizes a laser stripe grid with cutting edge optics and is specifically designed for inspecting and measuring fastener flushness, countersink alignment and dielectric fill height. Surface maps are displayed in real-time on the color LCD, and measurements are extracted and simultaneously written to the data table.
Download Product Datasheets
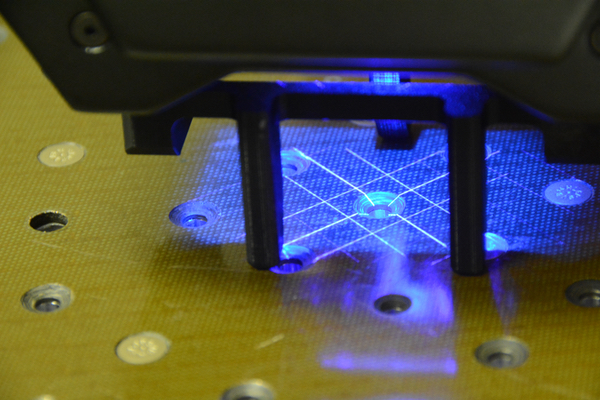
LEARN MORE ABOUT THE HS742 3D CROSS-HATCH LASER SENSOR
FEATURES & APPLICATIONS
The HS742 is battery powered and portable
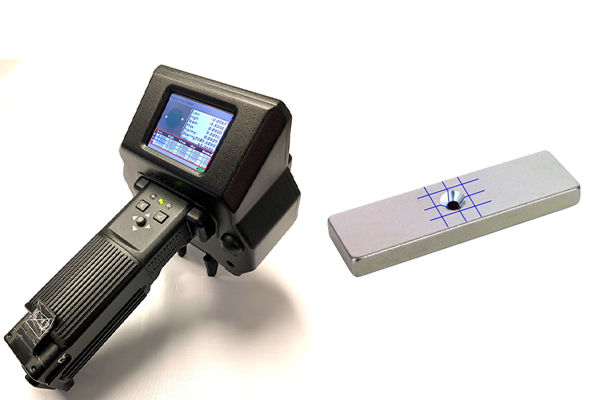
- Field of View Options: 1.20” x 1.20” (30mm x 30mm) Scanning Region
- Display Size: 2.4” Horizontal
- Features include:
- Blue cross-hatch lasers
- 1270 scan points over sensor field-of-view
- 1 GHz DSP processor – measurements are completed in as little as ½ second.
- Totally self-contained – no need for external PC or cables for operation
- Automatic gain optimization – scanning on wide variety of colors/finishes
HS742 Applications
Application | Standoff |
---|---|
Aerospace Countersink – composite or metal, flat or curved | Countersink |
Aerospace Fastener – composite or metal, flat or curved | Fastener |
Aerospace Dielectric Fill – composite or metal, flat or curved | Fastener |
FIELD OF VIEW & LASER OPTIONS
Field of View Options
FOV Option | Field-of-View | Scanning Grid Resolution | Diameter Range | Accuracy |
---|---|---|---|---|
-F20 | 1.20” x 1.20” (30mm x 30mm) | 0.0015” (38µm) | 0.250” to 0.625” (0.635mm to 15.87mm) | +/- 0.001" (25µm) |
-
Scanning Technology
The HS742 Sensor model is available with 3D Cross-Hatch Scanning technology. Learn more about how LaserGauge® scanning works.
-
Blue Laser Technology
Blue laser technology works accurately on various surfaces including painted, unpainted, translucent, transparent, some plastic, composite, and shiny.
Laser Safety Warning Label
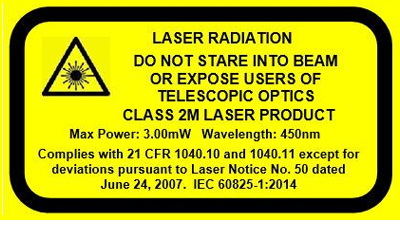
VIRTUAL GAUGES
Virtual Gauges that come with the HS742
"Virtual Gauges" are the mathematical algorithms used to process a scan and extract measurements from it. The following Standard Virtual Gauges are provided as a part of the preloaded configuration for both the HS702 and HS703 and are used mostly for Gap/Flush and Sheet Metal applications in the automotive industry.
- Countersink
- Fasteners
- Dielectric Fill
Custom Virtual Gauges can be developed/created according to customer requirements and measurement methodology upon request. Learn more about Standard and Custom Virtual Gauges.
Measurement output includes numerical and graphical displays as well as auditory feedback
-
Display Output
Numerical and graphical results are displayed and can indicate in- or out-of-spec conditions. Operation feedback is provided to assist the operator in obtaining the best measurements. -
Auditory Output
A variable volume speaker will sound different tones to indicate in- or out-of-spec measurements, errors or misreads, and low battery. -
Data Output
All processed scans and the extracted measurements are automatically saved to the sensor memory for later retrieval. When the sensor is plugged into a PC it will map the data memory as a drive, much like a USB memory stick so that retrieving files is fast and easy.
SPECIFICATIONS
HS742 Specifications
-
User Input
2 sets of 3 LED’s, 5-Way Joystick and 2 Buttons -
Communications
Wireless - 2.4GHz ZigBee module with ZigBee USB Stick for computer Cable - USB 2.0A to Mini 5-Pin USB, 6’ -
Processor
1GHz Speed -
Memory
8GB of data/scans/routines -
Battery
High capacity, rechargeable lithium-ion Inspired Energy series NB2037
-
Shock Protection
Cast urethane housing -
Environment
0° - 70° C -
Size
5.13" (w) x 4.88" (h) x 8.56" (l) -
Weight
23 oz. (27 oz. with battery) -
Display
2.4” Color Display -
Touchscreen
No -
Scan Type
3D Cross-Hatch -
Laser Color
Blue -
PC Software Interface
LGTools, Windows™ compatible
ACCESSORIES
HS742 3D Cross-Hatch Sensors come standard with the following:
- Sensor
- 1 Countersink Standoff with 3 different countersink angle blades
- 1 Fastener/Fill standoff
- Zigbee Wireless USB Dongle
- Battery charger
- Accessory software (LGTools and LGCommander) link to software pages
- 6’ Cable – USB 2.0A to Mini 5-Pin USB
- Hard-shell carrying case
- 1-year warranty
-
Optional Accessories
- Holster
- Standoffs
-
Included Software
- LGTools – this application sends, retrieves, and formats data from a computer to the DSP Sensor via USB cable or ZigBee.